Parkdale Mills is the world leader of spun yarn and fiber innovation. Based in Gastonia, North Carolina, they produce 18 million pounds of fiber yarn per week for clothing brands, military apparel, home textiles, carpeting and other products. When the global health event hit in 2020 and the demand for production decreased by about 75 percent, the team at Parkdale Mills was determined to find a way to maintain operations and keep their people employed. Learn how they were able to show resiliency and overcome this challenge, turning it into a heroic initiative their whole company would be proud of.
In times of crisis, that's when you really know who you can trust, who you can rely on. I can say today that ADP was, and still is, one of our truest and strongest partners.
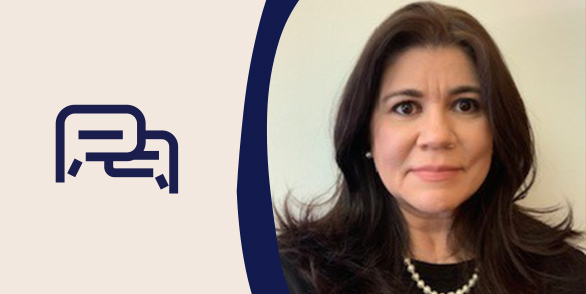
Karen Menting,
VP of HR
Parkdale Mills
Challenges
- Maintaining operations, staying up to date with ever-changing compliance regulations and keeping their people employed during a global health event that significantly impacted their industry.
How ADP helped
- ADP provided ongoing resources and communications regarding compliance regulations during the global health event. Additionally, ADP RPO helped Parkdale Mills recruit the necessary headcount to support operations during this challenging time.
Why ADP
Karen: One of the reasons we decided to go with ADP back in 2017 was not for the business we have, but for the business we want. The tools ADP provides us serve as an enabler for us to be more strategic. We now have the statistics and modules that provide us the real-time information we're looking for right at our fingertips. It makes my role a lot easier to focus on what matters most – our people.
Overcoming challenging times
Karen: 2020 was possibly the craziest year in our lives. In addition to a global pandemic, we saw the dramatic downturn in the economy, civil unrest, fires, earthquakes, hurricanes and even a presidential election. One or more of these events really touched all of us in one way or another. Survival was a crucial order of business for us. We tried to keep our facilities open as long as we could. But we, like other companies, felt the shock of the pandemic. With the shutdown of many retail stores, it also directly affected the demand of cotton apparel. We were forced to shut down many facilities because of the downturn and thousands of associates had to be furloughed because of these unprecedented times.
But then, the White House reached out to our CEO, Andy Warlick, expressing the need for PPE, particularly face masks and isolation gowns. Within two and a half days, Parkdale had a commitment of 600 million face masks. Imagine, this PPE project allowed thousands of textiles and supply chain workers to come back to work. This was real, and we didn't have time to dwell. We had a commitment to protect our associates and their health and deliver on our promise to the American people – and we were able to deliver.
ADP’s help through the global health event
Karen: We relied heavily on support from ADP and their consistent stream of communications regarding COVID-19. The Employer Preparedness Toolkit helped us navigate the overall effect on the workforce. It also helped us understand the latest legislative updates to the ever-changing COVID landscape. The COVID Employee Communications Toolkit is the tool I've really used the most. Having all this information right at our fingertips was crucial and it enabled us to focus on the unique challenges and opportunities, as well as the health and safety of our associates. We also leveraged Eye on Washington because it was important to learn and understand if our associates were able to benefit from everything that was included in the CARES Act.
I particularly trusted the information that was being provided to us through ADP. It gave me an opportunity to work out in the field, take care of our people and continue strategizing. We received a lot of information from many sources, but for me, the most credible information was what was provided to us through ADP.
John: Once we realized the pandemic was here, we needed to adapt how we operated. We did everything that was recommended, because we were really worried that if COVID occurred in our plant, it would spread rapidly. We kept everyone six feet apart, we removed half the seating in our canteens, we required face masks, we put up partitions in our breakrooms. We already required hand sanitizing because of being in consumer products, so that was easy, but we took a lot more care in placing more containers of hand sanitizer out on the production floor. We limited any outside people from coming in so if we had a case, we could do some contact tracing. We put portable toilets outside so truck drivers didn't have to enter the building. We hired additional cleaning staff so they could sanitize anything that might be touched.
Because of our efforts, we were able to keep the virus out of our largest plant in Cleveland to a great degree. We never had more than five or six people positive at any given time, and as far as we know, no one was infected within the plant – it all came from the outside. And we have no cases as of today, in manufacturing or in our offices.
Read the full story, click the link below.