Based in Augusta, Georgia, FPL Food LLC is proud to supply top-tier Georgia-grown beef to retail, food service, and food manufacturing partners around the nation and the globe. With five farms, including four cattle farms and one crop farm, FPL Food operates on 3,500 acres and has 1,450 employees.
Their HR operations team is led by HR Manager Jeffrey Saxon, who spearheads employee operations at their main location in Augusta, and HR Manager Guy Smith, who leads HR operations at their Thomasville location.
I don’t know of any other system that has the abilities that ADP does, and it’s still user friendly.
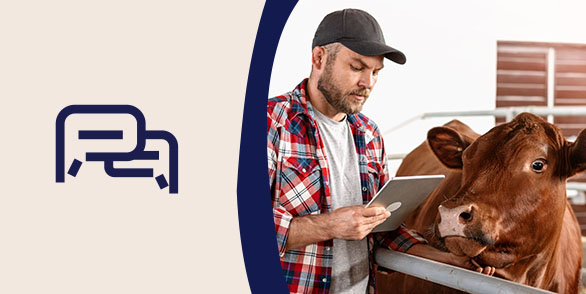
Jeffrey Austin Saxon II,
HR Manager
FPL Food
Challenges
- The messy manufacturing environment was not conducive to traditional timeclocks requiring a thumbprint or badge
- Manual work was required to correct errors or update time when clocks were down
- Unreliable punching and error-prone manual recording introduced errors in payroll processing
How ADP Helped
- By partnering with Oloid through ADP® and ADP Marketplace, Jeffrey, Guy, and the team at FPL have transformed their clocking practices, empowered managers and employees with a more efficient process and streamlined payroll with punches that flow effortlessly into their ADP payroll system.
ADP Solution
- ADP Workforce Now®
A unique environment in need of reliable technology
The beef manufacturing industry is unique, specifically within the production environment. Workspace conditions can be messy and demanding, affecting the reliability of traditional time-punching systems that require a badge swipe or a thumbprint. Workstations often include a significant amount of moisture and water, and the existing systems were not robust enough to withstand the frequent exposure to these elements. This led to frequent issues with clocking. What’s more, their work also requires special clocking capabilities for employees taking on and off their personal protective equipment.
“Our biggest issue was that the clocks we were using before were constantly breaking down due to our working environment," says Jeffrey. This led to inconsistencies in time tracking, extra work for managers to track time manually and employee frustration, impacting overall productivity. Badges can also be lost or passed around. Guy shared this sentiment. “People lose their badges all the time,” he says. “It’s also hard to get a picture of who’s in the building at any given time if employees lose their badges or hand their badge to another worker to clock in on their behalf.”
Biometric time clocking that requires a finger- or thumbprint was also challenging because of the work environment. "Getting a clean fingerprint just isn’t always realistic,” says Jeffrey. “Plus, the reader was always dirty, making it unable to read fingerprints anyway. We just couldn’t find anything that worked for us.”